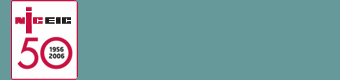 |
|
|
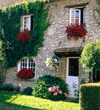
|

There
are precautions which can be taken to prevent danger from the
use of portable electrical equipment in hotels and tourist
accommodation. Many different areas of work are found in
hotels - some are low risk, like offices and bedrooms, some
are higher risk, like kitchens and laundries.
|
 |
HSE
Inspectors may decide to carry out a health and safety
inspection and they have powers to enter at any reasonable
time. They may ask you how your business deals with electrical
dangers. Following a simple plan of inspecting and testing
will help show that you have an effective system for
maintaining portable equipment.
Portable equipment is
equipment that has a cable and plug, and can be easily moved
around such as kettles, heaters, fans, lights and televisions.
Equipment in hotel bedrooms with a permanently wired lead like
hairdryers or kettles also comes into this category. There may
also be kitchen equipment such as mixers and food processors,
laundry equipment and maintenance equipment. The legal health
and safety requirements are restricted to equipment within the
hotel management's control and does not include electrical
equipment brought in by guests.
The risks from
portable electrical equipment used in hotel bedrooms and
offices are low, but the leads and plugs, and sometimes the
equipment itself, can become damaged. This may result in an
electric shock or may cause a fire.
Most faults or
damage can be found by visual inspection. After disconnecting,
the signs to look out for on the equipment, cable and plug
are:
• |
damage, such as cuts
or abrasions to the cable covering;
|
• |
damage to the plug
such as the casing is cracked or the pins are bent;
|
• |
non-proprietory
joints, including taped, in the cable;
|
• |
the outer covering
of the cable not being gripped where it enters the plug
or equipment. Look to see if the coloured insulation of
the internal wires is showing;
|
• |
equipment that has
been used in conditions where it is not suitable, such
as a wet or dusty workplace;
|
• |
damage to the outer
cover of the equipment or obvious loose parts or
screws;
|
• |
overheating (burn
marks) | A formal inspection could
also include removal of the plug cover to check:
• |
the cord grip is
holding the outer part of the cable tightly;
|
• |
the wires, including
the earth wire where fitted, are attached to the correct
terminals;
|
• |
no bare wire is
visible other than at the terminals;
|
• |
the terminal screws
are tight;
|
• |
there is no sign of
internal damage, overheating or entry of liquid, dust or
dirt.
| Most of
these checks apply to extension leads and their plugs and
sockets.
It is not necessary to have an electrician
carry out this visual inspection. Any competent member of
staff can do it, with enough knowledge and training. Users
should also be encouraged to look critically at the equipment
they use, and to look for damage to the outside of the
equipment and its lead and plug before they use it, but they
should not take the plug apart.
|
However, some
faults cannot be detected by inspections, particularly
lack of continuous earths, and for some equipment the
earth connection is essential to safety. Therefore, all
earthed equipment and most leads and plugs connected to
equipment should also have an occasional combined
inspection and test to look for faults. Combined
inspection and testing should be carried out where there
is reason to suspect the equipment may be faulty,
damaged or contaminated, but where this cannot be
confirmed by visual inspection. Combined testing should
also be carried out after any repair or similar work to
the equipment. Suggested intervals are shown below.
|
Equipment/environment |
User checks |
Formal visual inspection |
Combined inspection &
testing |
Battery operated |
No |
No |
No |
Extra low voltage:
telephones, low voltage desk lights |
No |
No |
No |
IT: desktop
computers, screens |
No |
2-4 years |
No if double insulated - otherwise up
to 5 years |
Photocopiers, fax
machines: rarely moved |
No |
2-4 years |
No if double insulated - otherwise up
to 5 years |
Double insulated
equipment: moved occasionally e.g. fans, lamps |
No |
2-4 years |
No |
Double insulated
equipment: handheld e.g. some floor cleaners |
Yes |
6 months - 1 year |
No |
Earthed equipment:
e.g. electric kettles, some floor cleaners |
Yes |
6 months - 1 year |
1-2 years |
Cables and plugs connected to
the above.
Extension leads (mains voltage) |
Yes |
6 months - 4 years depending on
equipment connected to |
1 - 5 years depending on equipment
connected to | Keeping
records of the results of inspection and testing can be
useful, and can prove important should there be an accident.
|
|
Extension Leads The use of extension
leads should be avoided where possible. If used, they should
be tested as portable appliances. It is recommended that
3-core leads (including a protective earthing conductor) be
used.
A standard 13 A 3-pin extension socket-outlet with a 2-core
cable should never be used even if the appliance to be
used is Class II, as it would not provide protection against
electric shock if used at any time with an item of Class
I equipment. See Glossary for explanations of Class I
and Class II equipment.
Only competent contractors should be employed to carry
out electrical work in hotels. The NICEIC maintains a
Roll of Approved Contractors capable of safe, good quality
work. |
|
| |